这是最简单的分类方法,如农业用液压系统、船舶用液压系统等,本书就是按这一原则分类的。这种分类方法的优点是从名词就可看出其应用场合,缺点是看不出该液压系统的特点及要完成的动作。
按液压介质的循环方式可分为开式液压系统和闭式液压系统:
(1)开式液压系统
如图1. 3-1所示,液压泵自油箱吸油,供给液压缸或液压马达作功。而液压缸或液压马达的回油则流回油箱。
开式液压系统结构简单,油箱是系统中介质的吞吐和存贮场所。油液在油箱中能散热冷却和沉淀杂质,开式系统中的液压缸或液压马达在制动或换向过程中,外负载的惯性运动所产生的能量是不能回收的,只能消耗在制动过程的发热上。
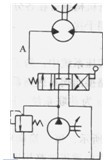
图1. 3-1 开式液压系统
(2)闭式液压系统
图1. 3-2所示为一典型的闭式液压系统。液压泵a的进出油口与液压马达b的进出油口分别用管道连接。马达的回油不回油箱而直接进入液压泵的吸油口,形成闭合回路。操纵液压泵a的变量机构可改变液流的方向,从而使马达换向。为使闭式液压系统正常工作,除了液压泵与马达组成的主回路以外,还须有一些元件组成辅助回路。阀1~5组成双向安全阀,防止管A、B内的油压超过单向阀3的调定值。为补充系统的泄漏,还须设置一个辅助的小泵c,其工作压力由溢流阀6调定,应略高于液压马达的背压,而液压泵c的流量应略高予系统的泄漏量。液压泵C输出的油经过滤器、单向阀1或2补充到系统的低压边,多余的流量经溢流
阀6流回油箱。
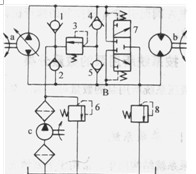
图1. 3-2 闭式液压系统
闭式液压系统结构较复杂,但油箱容积小,结构紧凑。马达有背压直接供入泵的吸油口,降低了对液压泵的自吸性能的要求。而开式液压系统的马达背压不能供给液压泵的吸油口而只能变成热能在背压阀中白白消耗掉。
闭式液压系统制动过程可通过操纵泵a的变量机构使排量逐步变为零而实现的。在此过程中,外负载的惯性力变成主动力,拖动液压马达b成为液压泵工况,将油流输给液压泵a,使液压泵a呈液压马达工况而带动发电机加速旋转而发电,输给电网中其他负载。故外负载的惯性能可以通过液压马达b变成液压能输给液压泵a变成电能而回收。同样负载在重力作用下下降的工况,执行机构在重力作用下呈液压泵工况而把重力下降的能量变为液压能推动液压泵a作马达运行,从而带动电机成为发电机运行而回收液压能。但液压泵由内燃机拖动
时,则不能实现功率回收。
由上可见,开式液压系统适用于功率较小的机构,内燃机驱动的移动式机构(如铲车、高空作业车、液压汽车、起重机、挖掘机等)以及固定式机构上。而闭式液压系统则适用于液压泵由电动机驱动的下述机械:外负载惯性大且换向频繁的机构(如起重机的旋转、运行机构及龙门刨床、拉床、平面磨等往复工作台);重力下降机构(如不平衡类型的起升、动臂摆动机构等);外负载惯性力大的重力下降机构(如平衡型起重机的变幅机构等)。闭式液压系统也适用于要求结构特别紧凑的移动式机械上(如液压汽车、拖拉机及矿车等的运动机构上)在大型轮船的舵机的泵控马达系统上也常用闭式液压系统。
在发热量较大的闭式系统中,为改善系统的散热情况,需增加补油量,故增设低压选择阀(图1. 3-2中的阀7),使系统经常有部分低压油经阀7排回油箱。但此时辅助泵c的流量应是主泵a的流量的20%~30%。
1.3.3按一个液压泵所驱动的执行机构的
数量和形式分类
1.3.3.1独立式系统
当一个液压泵只向一个执行机构供油,就称为独立式系统。
1.3.3.2组合式系统
一个液压泵向几个液压执行器供油,称为组合式系统。组合式系统又可分为以下四种:
(1)并联系统
如图1.3-3所示。液压泵排出的油同时向两个或两个以上的执行器供油,而其回油则分别回油箱。这种系统的特点是各执行器的速度随负载变化而改变。负载大,则速度减小。因此并联系统只适合于外负载变化较小或对执行机构运动速度要求不严的场合。
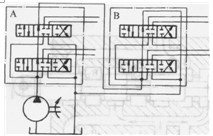
图1.3-3并联系统
(2)串联系统
如图1. 3-4所示,一个液压泵向2个或2个以上的执行机构供油。液压泵向第一个执行机构供油,以后机构的进出油口依次顺序相联,而最后一个执行机构的回油则流回油箱。
.jpg)
图1. 3-4 串联系统
串联系统中,后一液压执行机构的输入流量等于前一执行机构的输出流量,故串联系统中执行机构的运动速度基本上不随外负载而变化。泵的流量在并联系统中被分别供应到几个执行机构,故在相同情况下,并联系统要求的流量比串联系统要多。但并联系统要求的液压泵的油压则比串联系统小。
目前中小型液压起重机、高空作业车及小型挖掘机等大多采用串联系统,使各机构可以同时动作而且互不干扰。提高了作业速度,简化了系统。但串联系统的液压泵压力负担较重,故重载时不宜采用。在大多数机床、注塑机等液压系统中常采用并联系统,这可使液压泵的压力负担较小,对有些要求同时动作的执行机构则可在各分支系统上设置节流装置以防止互相干扰。
(3)独联系统
在工程机械液压系统中,为了简化管路,使结构紧凑,常用多路换向阀来达到系统油路的不同连接方式。图1.3-5a为并联系统,b为串联系统,c为独联系统。
如图1.3-5c所示,每一换向阀的进油腔与其前一换向阀的中立位置进油路相连,而各阀的回油管则同时与总回油管相连。这样各阀控制的液压执行机构就互不相通,一个液压泵在同一时间只能向一个执行机构供油,故称为独联系统,系统中液压泵的压力和流量按各执行机构单独工作时最大压力及最大流量来决定。
(4)复联系统
复联系统是以上三种系统的组合,如并联一独联、串联一独联、串联一并联等系统。图1. 3-6为并联一独联系统。多路阀A控制一部分并联的液压执行机构。多路阀B则控制另一部分并联的液压执行机构。但两个多路阀所控制的执行机构之间是相互独立的。所以在B阀操纵的执行机构动作时,即使误操作A阀,也不会使A阀控制的执行机构误动作。
图1. 3-7为串联一独联系统。多路阀A控制的执行机构互相串联,多路阀B控制的执行机构也互相串联,这两个串联系统之间则由阀1使它们相独联。这样在B阀操纵的执行机构动作时,不致因误操作A阀而引起A阀控制的执行机构误动作导致事故。
1.3.4按系统所用泵的数量分类
按液压系统所用泵的数量可分为单泵系统和多泵系统。
1.3.4.1单泵系统
单泵系统结构简单,常用于下列情况:
(1)功率较小,工作不太频繁的一些开式系统,如16t以下中小型液压汽车起重机、高空作业车、铲斗容量0. 4rri3以下的小型半液压挖掘机、小型铲车等。
(2)功率较小,外负载惯性较小的一些开式系统。如小型机械手、磨床等要求精确换向、定位的系统。为此要求运动有减速过程。半自动车床中要求有些机构有快进和工进两种速度。这些机构都宜用节流的方法来调速和减速缓冲,由于功率较小,故温升或冲击不会太大。
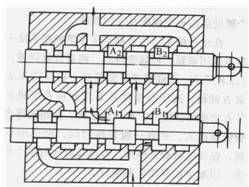
.jpg)
a)
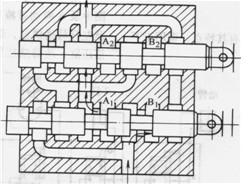
c)
(1).jpg)
图1:3-5 多路换向阀系统
.jpg)
图1. 3-6并联一独联系统
伸缩 变幅 支腿
.jpg)
图1. 3-7 串联一独联系统
1. 3.4.2多泵系统
多泵系统结构较复杂,但有其特点,常用于下列情况:
(1)用于单回路系统
由图1. 3-2可知,闭式系统有一个主泵并有一个辅助泵以补充泄漏及冷却系统。
在组合机床、半自动车床等单回路系统中,有时也采用双泵。轻载快进时,两泵合流供油,如图1. 3-8所示。重载慢进时卸荷阀1打开低压大流量泵A卸荷,高压小流量泵B单独向系统供油,以节省功率降低温升。有些油压机、注塑机等也要求快慢速比大,并有一段保压时间,则也用双泵系统,在快速时双泵供油,慢速及保压时单个小泵供油,以减少功率消耗和温升。
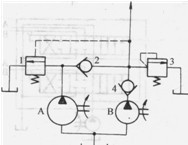
图1. 3-8双泵供油回路系统
(2)用于多回路系统
图1.3-9为采用双泵的挖掘机液压系统简图。图中泵A向动臂液压缸、斗杆液压缸、回转马达及左行马达供油,组成一独联回路;泵B向铲斗液压缸、动臂液压缸、斗杆液压缸及右行马达供油,组成另一独联回路,故为双回路系统。这两回路本身及两回路之间都不互相干扰,从而使分属于这两回路中的任意两机构在轻载及重载时都能实现无干扰的同时动作,提高挖掘机的生产率和发动机的效率。
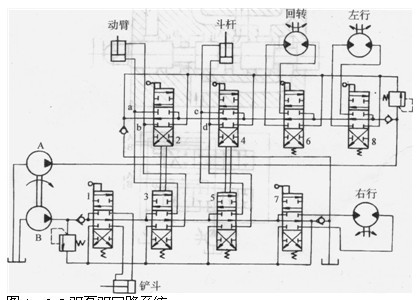
图1. 3-9双泵双回路系统
1.3.5液压功能回路
上述1.3.1、1.3.2、1.3.3、1.3.4各节的分类方法是根据整个液压系统的特点来分类的。而一个液压系统要完成主机的动作,必须同时具备几种功能。例如图1. 1-1所示的系统,为了使液压马达正反向都能转动,就必须有换向阀,为了保证系统的安全,不超压,就必须有安全阀。又如图1.1-2所示系统,为了保证系统安全,须设置阀1~5所组成的桥式回路,使系统压力不超过阀3的设定值,为保证补油泵多余流量能溢流,须设置溢流阀6。所以我们还可从完成不同的功能这一角度对整个液压系统进一步分解。一个完整的液压系统可以分解为几个功能回路。这种功能回路分别完成不同的功能,从而使整个系统完成主机要求的动作。按所完成的功能不同来分类的回路称为功能回路,也称为基本回路。
按功能来区分回路的最大优点是便于液压系统的设计及分析。一个液压系统的功能不外乎压力调节、速度调节及方向调节。在设计一个系统时把几种基本回路组合起来就可以完成所要求的动作。关于功能回路的详细分析,在第3章中叙述。